
Specifications
Die sleeve inner diameter
|
8 mm (0.31 inches)
|
Die sleeve outer diameter
|
45 mm (1.77 inches)
|
Typical force for quality pellets
|
390-1,170 lb (0.18-0.53 ton, 1.73-5.20 kN)
|
|
75mm height | |
Die sleeve height | 40 mm (1.57 inches) |
75mm (2.95 inches)
|
Assembled height with spacers (w/o powder)* | 91 mm (3.58 inches) |
129 mm (5.80 inches)
|
Assembled height no spacers (w/o powder)* | 81 mm (3.19 inches) |
109 mm (4.30 inches)
|
Typical Max pellet length**
|
15 mm (0.60 inches) | 35mm (1.40 inches) |
D2 Tool Steel | Stainless Steel | |
Yield Strength | 80,000 psi (550 MPa) |
160,000 psi (1100 MPa) |
Recommended max loading (@ 50%) | 40,000 psi (275 MPa) | 80,000 psi (550 MPa) |
Recommended max force |
3,100 lb (1.41 ton, 13.84 kN)
|
4,650 lb (2.12 ton, 20.77 kN)
|
Typical force for quality pellets
|
390-1,170 lb (0.18-0.53 ton, 1.73-5.20 kN) |
*If making thicker pellets, the die set can operate just the same without spacers.
**Pending on the material you are pressing with and the method of loading the die set.
Recommended max force = Is the maximum force you can put the die set under. This includes a 50% safety margin which is industry standard.
Typical force for quality pellets = This is the range we recommend using that will get you a great pellet and is much less than the recommended max force.
Each Die set Includes

Item | Description | Quantity |
---|---|---|
1 | Plunger | 1 |
2 | Spacer | 2 |
3 | Die Sleeve | 1 |
4 | Support Plate | 1 |
5 | Ejector Sleeve | 1 |
-
Precision Made, Individually Inspected
-
FREE DIE SHIPPING USA, UK & EUROPE
-
Worldwide Shipping
-
HARDENED STEEL, MIRROR FINISH
-
Superior Design
-
HIGH TOLERANCE MACHINING
Description
Pellet Die set for making 8 mm (0.315 inch) pellets from powders.
8 mm Pellets Dies have a range of applications. As with 6 mm die sets, 8 mm pellet dies are commonly used for making KBr pellets for FTIR analysis, in which small quantities of powders are mixed with Infrared-transparent KBr (Potassium Bromide) powder before pressing into a pellet and transferring into the FTIR.
High compressive stresses can be applied to powders in the 8 mm pellet die sets using low pressing forces. Whilst this can be useful for quickly making pellets, always stay under the recommended load and make sure you stay safe. If you don't have a hydraulic press, for the lower diameter die sets, pressing force can be applied manually with a lever press or arbor press. If you need a slightly difference size for your application.
Materials
D2 Tool Steel: For most pellets this material will be perfect for the job. Hardened D2 tool steel (Rockwell hardness >C60) for long lasting trouble free performance. The sleeve is polished to high tolerance to allow hardened tool steel plunger to slide through perfectly. Plungers and spacers are made from high yield strength steel, machined and polished to high tolerance for the perfect fit. Interior surfaces are ground to mirror-like finish. Release ring is made of aluminum.
Stainless steel: For a die set with great corrosion resistance and with for those heating for heating their dies up to max 250°C (482°F), this is a great choice. Stainless steel is a more expensive starting material and is slower to machine which leads than a slightly higher costs than our regular die sets. Our stainless die sets are heat treated for high hardness (~58) and have extremely high strength (160, 000 psi).
Product Video
Pressing Loads

Safety
- Always wear googles and safety protection equipment.
- Always press using a safety guard.
- Do not apply pressure above what is shown on table above.
- Make sure the plunger is fully engaged before pressing.
- More force does not always mean better pellets.
- Increasing with a higher force increases the chance of breakage.
Shipping and Returns
Most of the common die sizes are in stock in both our US and UK warehouses and we aim to have shipped out within 24-48 hours.
Free Die Set Shipping USA, UK, Canada and EU: Shipping is offered free across the USA, UK, Canada and EU for all die sets. In the USA and UK this typically takes 3-5 business days to arrive and is a tracked service. In Canada times vary depending on your local postal service. You will receive the tracking number automatically by email once your order has shipped.
Expedited delivery: Faster delivery options are available. Below are some indicative prices. To get the cost for your package and location, just add your address at check out and select the shipping option you want to check.
- USA FedEx 2 day delivery: typically $25-$65 USD depending on weight.
- USA FedEx Overnight Delivery: typically $40-$85 USD depending on weight.
- Canada FedEx International Priority: typically $25-$40 depending on weight.
Rest of Worldwide Shipping: Shipping costs to the rest of the world will be calculated at check-out. Please be aware that delivery times and tracking information vary for each country. Customs charges may apply and are payable by the buyer.
Returns: We offer a full refund on die sets that have not been opened or used. For safety reasons we can only accept a return of un-used die sets.
FAQ's
What is the max load for my die?
The max recommended load for the (product title) is 40,000 psi (275 MPa) for the D2 tool steel and 80,000 psi (550 MPa) for the stainless steel die set. These loads have a 50% safety margin, loads for each die set should be carefully considered before using the die to ensure safe operation. This is of particular concern with the smaller ID dies where you can reach the yield strength of the steel with a few pumps of the hydraulic press. Do note that using high pressing force does not guarantee a denser pellet. If you press too hard, you will most likely surpass the fracture stress of the compact well before you reach the yield stress of the material. The stress in your pellet will concentrate at the top side of your pellet and you will likely see cracking or "capping" at the top of your powder compact.
The typical force for making a good pellets can be found on the specifications table above.
Can I heat up my die set?
Our D2 tool steel die sets cannot be heated as the metal has been heat treated, heating it at all will compromise the heat treatment, making it softer, weaker and quickly lead to oxidisation.
The stainless steel die sets can be heated to around 250 °C (482F).
What is the thickest pellet I can make with my die set?
As a general rule of thumb your pellet height should not greatly exceed the diameter of your pellet. This is because you get non-uniform compaction through the pellet when you go thicker than the diameter, the top will get more stress concentration than the bottom (non-moving surface). That being said, all materials are different, so you can take this rule with a pinch of salt. The maximum height of pellets you can make using our standard range (50mm height die sleeve) die sets would be between 0.6-1.0 inch pending on the material you are pressing and method of loading the die set.
Tips
- If you’re pressing long pellets (with respect to your diameter), consider lubricating your die.
- Try adding a rubber o-ring (or something flexible) between the base plate and the die sleeve, this will allow movement of both he top and the bottom plunger, improve the stress uniformity through the pellet.
- For making very long aspect ratio pellets there are other methods such as isostatic pressing which might be more suitable. More information on this can be found here
Do I need to use lubricants or binders on my die set?
You do not need to lubricate your die before use for most materials nor do you have to use binders. Some people like to use a small amount on lubricant on the walls of the die as this is where there is highest friction during pressing and release which can lead to cracking. Likewise, some applications and materials use binders as common processing protocol. Both lubricants and binders can be burned out afterward when sintering above 700 °C (1290°F) leaving behind minimal residual residue (carbon).
How do I clean and store my die set?
After each use make sure die set is cleaned and dry. If you are storing your die for a long time or it will be exposed to moisture or humidity then you can simply spray with WD-40 or a similar product. If you are looking for a product to help with cleaning we recommend using 3M™ Creme Cleanser for cleaning our pellet die sets. It is a cream which can be used with water to clean our dies. The cream has a small amount of gentle abrasive to help remove chemicals from the surface. Use with a scourer coated sponge for best results. For inner surface of die sleeve, use with appropriate sized nylon brush.
The D2 tool steel we use are high strength and high hardness and typically the steel of choice for the most demanding tooling applications. If you don't dry it after washing or store it wet - yes it will rust. Don't worry, it happens - the good news is that it should be easy to clean off.
Advice for making good pellets?
There is a lot to say here...
- Number 1 - obviously - press safely, if unsure ask someone with experience. You are able to put a lot of force through your die with a hydraulic press. Think about the force you want to apply beforehand, do not exceed the force for the die you are using, wear safety googles with side shields, use a guard between you and the press, keep other items off the press table so they don't get caught, make sure everything is inserted correctly and well located before pressing.
- Check that your press plates are parallel and sample as level as possible before pressing. Check your pressure and force gauge is working and know what your max pressing force/pressure will be. Check against the maximum loads on the product page for your pellet die diameter.
- If the die is overfilled with powder before pressing, the plunger will not locate properly.
- Always clean your die before use - this will not only stop contamination but make the die work better, with less friction.
- Higher force is not necessarily better - if you find your pellet is cracking then you should consider using less force before using more force. Please can you make sure that anyone using this die set follows the recommended forces on the product pages on our website. Make sure that the force gauge on hydraulic press is working and accurate.
- If you are having trouble with a certain material - don't worry we have all been there. Consider drying before pressing changing the grain size your materials before pressing (more grinding), tapping with a small rubber mallet after assembly and before pressing (helps the powder move around, reorganise and settle before pressing), you can also try using lubricants or binders to help get your pellet out.
Have any questions? Feel free to reach out using our contact form.
Technical Help?
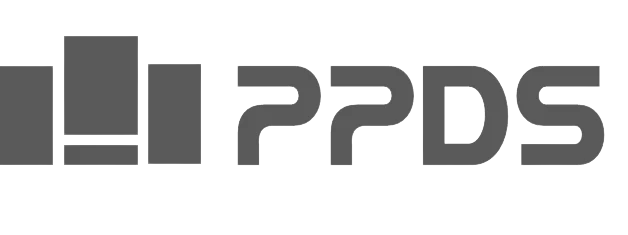
Dedicated technical support for all your project needs.
Contact us here